Model Making for Intricate Craft Molds
Mastering Precision in Model Making
Precision is the key to transforming ordinary molds into exceptional works of craftsmanship. Every groove, edge, and fine detail matters when crafting a master model, ensuring that the final mold captures the design’s full integrity.
To achieve this level of accuracy, the right tools and techniques are essential. Fine-tipped carving tools allow for intricate manual detailing, while CNC routers enhance precision, particularly for replicating complex patterns. Layering textures methodically can add depth and complexity, and maintaining sharp tools ensures clean, defined edges.
The importance of precision is best illustrated in real-world applications. Whether creating detailed jewelry molds or architectural models requiring perfect component fitting, refining these skills leads to professional-grade results. By studying successful projects and learning from experienced model makers, you can continuously improve your techniques.
As an Amazon Associate, I earn from qualifying purchases.
This post contains affiliate links. If you buy through them, I may earn a commission at no extra cost to you.
Selecting the Right Materials for Model Making
The foundation of a superior mold begins with choosing the best material for the master model. Each material offers unique advantages and considerations:
- Clay – Offers flexibility for hand-sculpting intricate designs but lacks long-term durability.
- Resin – Provides a smooth finish and is ideal for high-quality polished models.
- Wood – A stable base for larger models, though its grain may require surface treatment for detail preservation.
- 3D-Printed Materials – Enable precise, repeatable master models but require an investment in software and equipment.
Understanding how these materials influence mold longevity, wear resistance, and texture replication is crucial. Engaging in discussions with seasoned model makers through online forums can further refine material selection strategies.
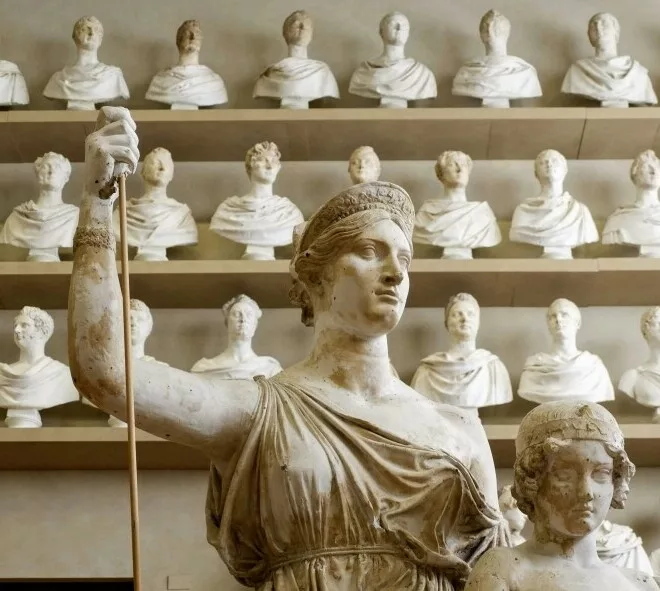
Advanced Sculpting & Finishing Techniques
Mastering sculpting and finishing techniques elevates the quality of molds, ensuring consistency and durability in production.
Sculpting Methods:
- Hand-Sculpting – Enhances artistic control, allowing for organic and intuitive refinement.
- CNC Routering – Delivers precision through automated carving, ideal for complex geometries.
- Digital Carving – Combines traditional techniques with digital precision for optimal results.
Finishing Techniques:
- Sanding & Smoothing – Eliminates imperfections, providing a clean, defect-free surface.
- Spray Coating – Enhances surface texture and ensures silicone or resin molds replicate details accurately.
Silicone molds capture surface details precisely, making surface preparation essential for professional-quality results.
Creating Multi-Part Molds for Complex Geometries
For intricate designs featuring deep recesses or undercuts, multi-part molds are essential to preserve shape integrity and simplify demolding.
Key Benefits of Multi-Part Molds:
- Prevents Breakage – Reduces stress on intricate details during demolding.
- Enhances Detail Preservation – Ensures complex designs remain intact.
- Facilitates Seamless Assembly – Precision interlocking sections prevent misalignment and distortion.
Designing molds with registration keys and alignment lugs ensures proper fit, maintaining accuracy throughout the casting process. Starting with small multi-part mold projects allows for a smoother learning curve before tackling large-scale, high-detail designs.
Enhancing Molds with Texture & Special Effects
Incorporating texture and special effects adds depth and realism to final castings, elevating the finished product’s visual appeal.
Effective Texturing Techniques:
- Silicone Skin Overlays – Create lifelike surface textures for enhanced realism.
- Etching & Engraving – Produce intricate patterns with precision tools or chemicals.
- Texture Stamping – Ideal for imprinting repetitive patterns on large surfaces.
Planning ahead ensures that textures transfer accurately from the master model to the mold, delivering high-quality results with minimal adjustments.
Reinforcing & Strengthening Molds for Longevity
A well-constructed mold should withstand repeated use without compromising detail or structural integrity.
Reinforcement Strategies:
- Fiber Reinforcement – Incorporate fiberglass or carbon fibers to strengthen the mold’s shell.
- Backings & Supports – Use metal or wooden frameworks for stability in large molds.
- Routine Maintenance – Inspect molds regularly for wear and perform repairs promptly.
Strengthening these molds ensures extended usability and reduces the need for frequent replacements, making the production process more efficient.
Leveraging 3D Printing & Digital Tools in Model Making
3D printing has revolutionized model making, offering unparalleled precision and repeatability. The integration of digital tools streamlines production, reducing manual labor while maintaining high-quality output.
Advantages of 3D Printing in Model Making:
- High Precision – Enables the creation of detailed, repeatable master models.
- Rapid Prototyping – Allows for quick testing and iterative design improvements.
- Hybrid Integration – Combines digital modeling with traditional sculpting for enhanced results.
Staying up-to-date with advancements in 3D printing technology and digital modeling software can provide a competitive edge, positioning artisans at the forefront of modern model-making innovations.
Conclusion: Elevate Your Model Making Expertise
By integrating precision tools, selecting optimal materials, refining sculpting techniques, and embracing digital advancements, model makers can push the boundaries of craftsmanship. Whether employing traditional hand-sculpting or utilizing cutting-edge 3D printing, the key to excellence lies in attention to detail and continuous skill refinement.
Next Steps:
- Experiment with new materials and techniques to refine craftsmanship.
- Engage with expert communities to stay updated on industry trends.
- Explore emerging digital tools to enhance efficiency and precision.
With dedication and innovation, your model-making abilities can reach new levels, ensuring exceptional results in every project.
Safety Tips for Model Making
Model making involves working with various materials, tools, and adhesives, making safety an essential consideration. Whether you’re using resins, clays, wood, or 3D-printed materials, following basic safety guidelines will help prevent accidents and ensure a smooth creative process.
1. Ventilation & Respiratory Safety
Many materials used in model making, such as resin, certain paints, and adhesives, release fumes that can be harmful if inhaled. Always work in a well-ventilated area, use a fume extractor when necessary, and wear a respirator mask when working with strong chemicals.
2. Protective Gear
- Gloves: Essential when handling resins, solvents, and sharp tools to prevent skin irritation or cuts.
- Safety Goggles: Protects your eyes from dust, splinters, or accidental spills.
- Apron or Protective Clothing: Prevents accidental spills on your clothes and skin.
3. Handling Sharp Tools
Craft knives, scalpels, and other precision tools should always be used with caution. Cut away from your body, keep your tools sharp (a dull blade is more dangerous), and store them safely when not in use.
4. Fire Safety
Certain adhesives, like super glue or epoxy, can be flammable. Keep them away from open flames, and always store them properly. When using heat-based tools like soldering irons or heat guns, never leave them unattended.
5. Safe Storage of Materials
- Store paints, resins, and adhesives in cool, dry places away from direct sunlight.
- Keep flammable materials away from heat sources.
- Always close lids tightly to prevent spills and maintain material quality.
By following these simple safety measures, you can enjoy model making while minimizing risks. Safety should always be a priority, allowing you to focus on the creative aspects without worry.
Contact Us
We hope you found this information on model making helpful! If you have any questions or need assistance, feel free to reach out. Please note that due to government regulations, you’ll need to sign in and confirm your message. We apologize for any inconvenience.
Author: Rob
Below is the platform I used to learn how to build this website and others.
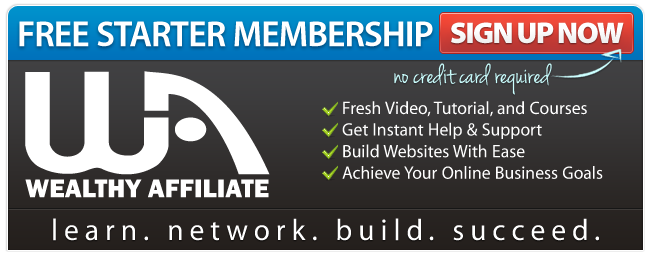
Thanks for the interesting article on techniques for model making and making intricate craft molds. You mention 3D printers becoming more popular and being used. Do you think that the art of making molds and models and even sculpting the traditional way will be lost as technology can easily mass produce models? I think now a days the masses don’t really appreciate the time and effort that goes into an artwork. I’d love to hear your opinion. I used to decorate cakes and all my designs were made by hand. I didn’t use shaped cake pans but carved the cakes by hand. My figurines were sculpted by hand and time consuming. I even made my own molds so I could get the right design but some potential customers didn’t appreciate skill and time involved in the work.
Hi Lyn,
Thank you for your comments and questions. 3D printers are a huge advancement, so yes many of the true methods of model making may disappear, but a new one is born because it is no easy task to draw and render the new type designs/models on a computer.
Many years ago I saw my first true model makers in a foundry environment where we were making parts for the auto industry and models were made to form patterns in the hand-packed sand before pouring the molten metal.
Rob
Hi!
This is a very interesting article! I think the art of making molds is very cool and I appreciate the talent of the artist. I had a favorite sculptor that made Christmas ornaments. He used to release one new design every year. He was a local guy that I would see at craft shows. His health declined as he got older and closed his business. I really miss his work, but I get to think of him every Christmas when I decorate my tree.
Your post is a fantastic deep dive into advanced model-making techniques! The breakdown of materials, sculpting methods, and reinforcement strategies is especially helpful for anyone looking to refine their craft. The section on leveraging 3D printing is particularly intriguing—combining traditional and digital techniques really seems to be the future of precision modeling.
When working with multi-part molds, what’s the best way to minimize visible seams in the final casting?
– Scott
Hi Scott,
Thank you for your positive comments and feedback, it is really appreciated. And yes, I think digital will control a lot of items. But an original carved piece will always be art.
Rob