Production 101 Garage Made to Phenomenal Growth
“Overview To My Cast Stone Adventure”
Production 101 & garage made to phenomenal growth all starts In the early 1990s, in the sunny state of Florida, where I found myself at a crossroads. For years, I had been exclusively installing wet cast stone—a craft that demanded precision and dedication. Before that, I had been a builder with many trades at my fingertips, including bricklaying, and always involved in construction, in one country or another. But now fate had other plans for me.
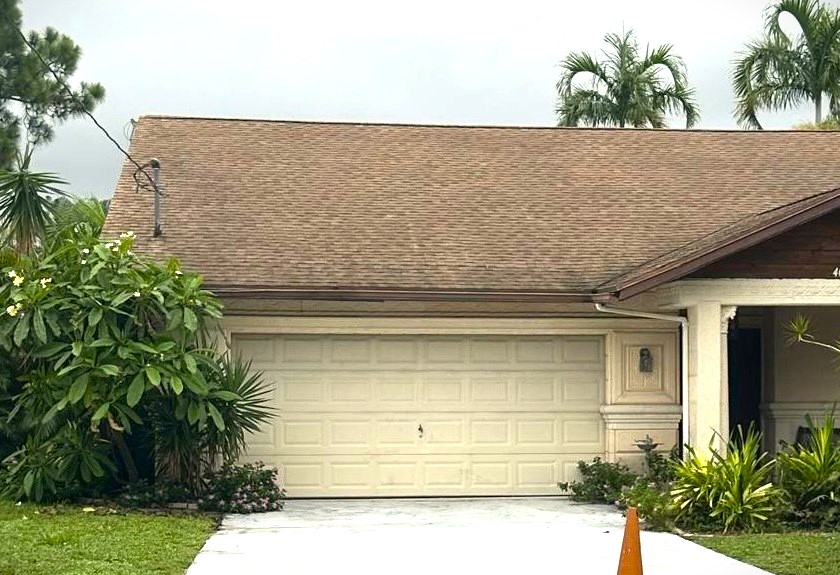
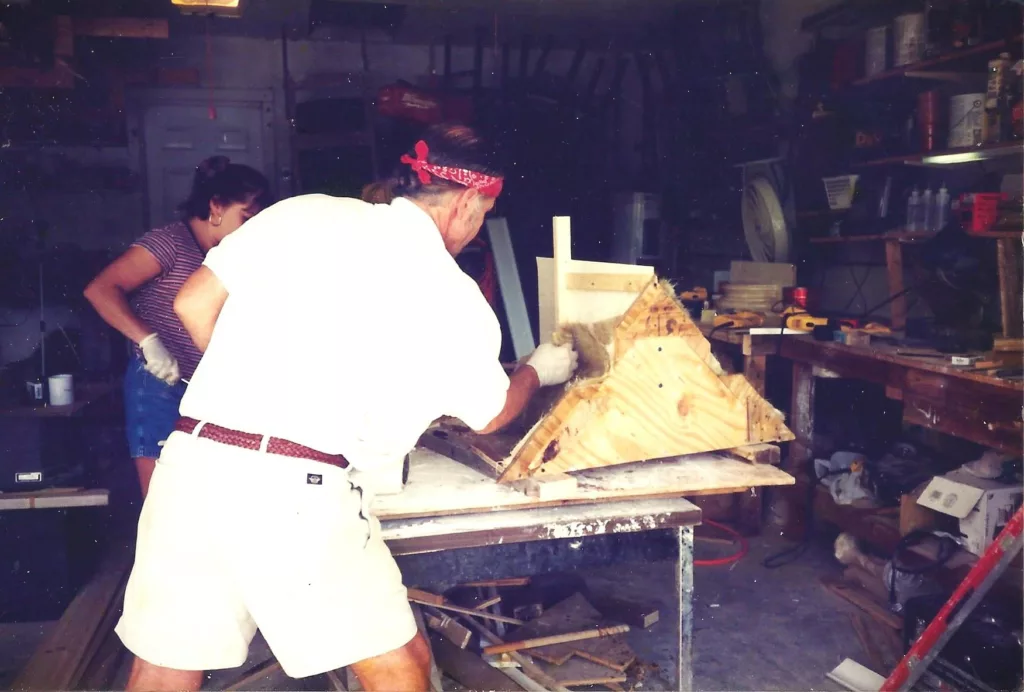
This post contains affiliate links. If you make a purchase through these links, I may earn a commission at no extra cost to you.
As an Amazon Associate, I earn from qualifying purchases
How It Happened, Day 1
One day, a customer approached me in a bind. Another company, the one I was currently working with, couldn’t supply the cast stone pieces they needed for nearly two months. The pressure was on, and I had a decision to make: Could I step up and create those pieces myself?
With confidence, I accepted the challenge. In the humble confines of my garage, armed with determination, my fiancee and a mixing drill, I set to work. Piece by piece, I crafted the cast stone pieces that would save the day. When the customer and their influential client saw the results, they were ecstatic. Little did I know that this seemingly small act would set the stage for something much greater.
From that pivotal moment, my journey took off. My garage made to Phenomenal growth just followed, year after year over the next six to seven years. I moved and expanded my operations four times, eventually occupying over 100,000 square feet of space at its peak. Our turnover reached an impressive £20,000,000 within my group of companies.
Basic Production Materials
If you’re venturing into the world of cast stone, you’re engaging with a tradition that blends art and engineering to create elements that enhance buildings and landscapes. Before you immerse yourself in this craft, or go forward to build or remodel a project using cast stone, it’s crucial to understand what cast stone is and why the right suppliers are integral to your success. Whether you are setting up a full-scale operation or working on a small project at home in your garage or shed, the same principles and needs apply. And if you just intend to buy the product then its better that you are fully informed.
What I Started Out With
But let’s rewind to the basics—the raw materials that fuelled this remarkable ascent. I started with just a few of my trusty tools: a mixing drill, a paddle, and a mixture of small tools, some powered, many not. and a keen eye for quality. White cement we purchased from Home Depot, and by the 112-pound bag, one at a time, but it became our lifeblood. We guarded it like gold dust, because the white cement price was a huge factor in our daily budget, knowing that each bag held the potential for progress. I had nightmares over the white cement price. If I remember it was $22 back then.
Hired My First Employee
When I hired my first employee, we celebrated a new milestone. Together, we invested in a modest Home Depot electric mixer. His joy was contagious, and our production soared. I continued to design molds and oversee installations, while he meticulously crafted the pieces. We even took on deliveries, building a seamless partnership.
Today, as I reflect on those early days—the garage, the determination, and the camaraderie—I’m reminded that success often begins with a single step. From those garage-made pieces to the vast enterprise we became, it all started with a willingness to say, “Yes, I can handle that.” and a dream.
Hard Work & Determination Does Pay
And so, my friend, remember this: Hard work, determination, and a touch of resourcefulness can transform the ordinary into the extraordinary. Your journey, like mine, is filled with untapped potential waiting to be realized. Now you can understand how I know so much about this industry. Admittedly my lifelong involvement with construction did help, particularly my bricklaying, carpentry, tiling and plastering abilities.
Architectural Cast Stone
Cast Stone is a refined architectural concrete building unit manufactured to simulate natural-cut stone, it can be used in unit masonry applications, or be applied as a surface treatment, which is more common in the USA. It’s found in an array of structures, from grand historical renovations to intricate garden ornaments. The making of cast stone is precise; it demands a mix of high-quality raw materials, skill, and technology.
A key part of cast stone production is knowing and sourcing your materials and tools. Whether you’re fashioning facades that echo time-honoured aesthetics or adding flair to a new design, having reliable suppliers ensures that your cast stone mixture is spot-on, your tools are up to the task, and your final products are up to scratch.
So, on this journey, production 101 garage made to phenomenal growth, your first step is to secure the foundational elements. Whether this is when starting out or when in expansion mode the raw materials are key to ease and quality. That’s going to include selecting suppliers for your raw materials, which isn’t just about price, but also about quality, consistency, and service.
Selection of Raw Material Suppliers for Cast Stone Mixes
Making cast stone requires a lot of quality ingredients to ensure the final product boasts both it’s beauty and durability. I’m going to guide you through pinpointing the right type suppliers for the essential raw materials that make up any premium cast stone mix. This isn’t just about finding the lowest price; it’s also about ensuring the materials you choose are up to par for creating your architectural masterpieces.
Aggregates
First up, you’re going to need to zero in on good suppliers that are as close as practical to your operation and one of the first was one of the backbone materials of my cast stone operation: sand and aggregates. So, originally when starting out, we used to go to a local distribution place like a ready mixed concrete facility and load up the F350 with whatever was needed on the day.
If the concrete producer was using the same material then I knew what the purity, grain size, colour were and so the quality. The color will vary depending on where you are located, and this product will contribute to the texture, color and strength of the final cast stone product. Not all sand is equal, so selecting the one that works for your needs and quality standards is truly important. And it needs to be a product that is readily available with an on-time delivery service.
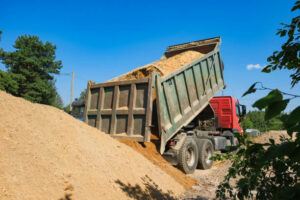
White Cement Supplier
A white cement supplier near me, and not just Home Depot was very important for logistics as volumes grew. But as this was the main cost ingredient in the production. Sand & aggregates you can nearly always find and create an easy workaround for. But good cement is critical, and not so easy to find and you cannot switch makes or suppliers in the middle of a contract as it can affect strength and colour far more than any aggregate. The bulk of the products I made evolved around the use of white cement.
We did have several projects over the years that used grey cement but they were a rarity.
There Is White Then There Is Other Whites.
Now when I say white cement did you know there is a spectrum of white types of cement available, some are virtually pure white and then there are others with various impurities in them. There are not many white cement manufacturers and suppliers. When I uncovered that information and I was aware of us having trouble maintaining colour on one quite large contract, I dug a lot deeper and analysed the mixing crew and process, I found the cause to be fine pieces of a blue particle in the white cement. It turned out this cement was from Holland and I was in Florida. So from then on, I was very particular about where I bought my cement.
Finenss Of The Cement
The other most important factor about cement is the Mls, this is a reference to the fineness of the cement, the finer the better the mix and colour disbursement, and in most cases the strength. The best white cement suppliers I ever used came from Colombia. Go figure, right?
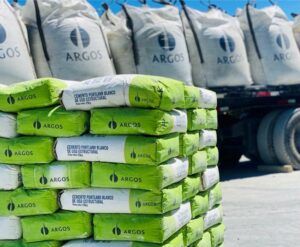
Next, the pigments. They give cast stone its varied and vibrant or subtle hues. You’re going to want pigments that come from a reputable manufacturer that operates a consistent manufacturing process. Many powdered pigments I have used are made and mixed from different powders with their secret formula which they give a name to. Then we as manufacturers would concoct our secret formulas. which made it difficult for the competition to replicate, in the long term value & availability of the provided pigments are the important points.
Mix Additives.
Additives can play a role in the mix as well. They can enhance the stone’s properties, like reducing the water content without compromising the workability or accelerating curing and demolding times. This means scouting for suppliers who have a range of additives and can advise on their use. Each additive you select should serve a purpose in your stone if you are going to use anything other than the basic. Just like too much of the pigments can weaken your mix or cause you to use more cement. There are a few other additives that if not used correctly can do the same.
Reinforcing Your Cast Stone
Concrete reinforcing fibres, non-ferrous. Over the years I learnt a lot of lessons. I started with different products that caused me inherent problems (mostly rusting), particularly with ferrous products, I evolved and eventually only used non-ferrous reinforcing, yes more expensive, but far fewer issues with hairline cracks or corrosion in just a few years later as with ferrous materials. Finding the right fibre is really important and can depend on your mixing methods and the quality of the labour that is batching the mixes, Many fibres can “clump”in the mix, others show through on your finished pieces, and if you are not careful you can end up with what I called “hairy stone”.
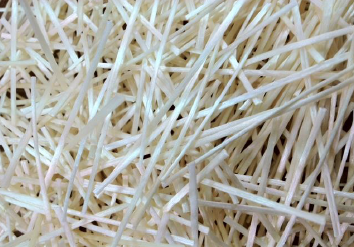
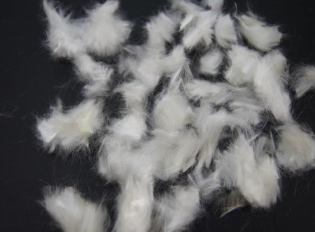
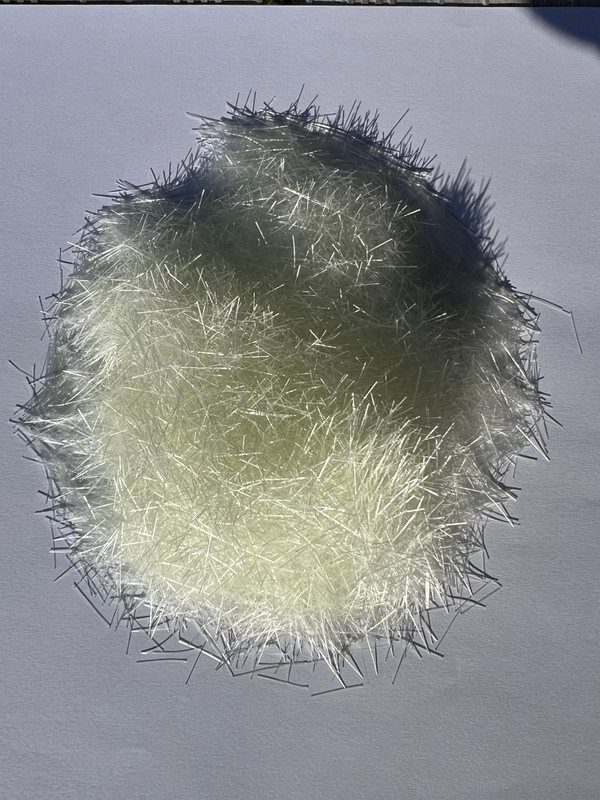
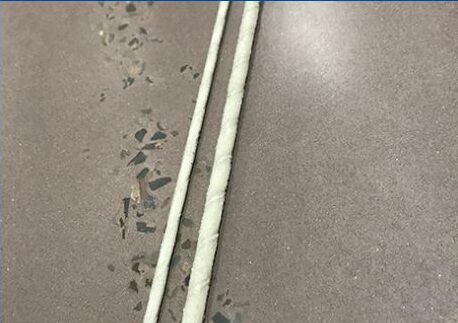
Fibreglass twisted rebar was a game changer for me, the smaller diameter rods, which came in 20′ (6m) lengths were perfect for making columns, especially when we incorporated some of the fibers too.
If we were making our wet-cast version of limestone, only a few things in the product manufacturing process were different. The quality of the molds, the type of raw aggregate we used and the exacting processes needed to complete the finish after the piece was demolded. We chose to use an aggregate with a lot of fine silica content that would shine through after the final processes, and normally we had to find that from a different supplier.
I will cover our approach and processes to this wet-cast limestone product in a later post.
Release Agents 101
Release agents can be very different for different finished products and what the mold is made from. A textured finish will be fine with a mixture of solid cooking fats and cooking oil, both are biodegradable, and smooth products are normally fine with a coat of cooking oil. while smooth products in RTV rubber molds may require special releases. Platsil silicone molds only need the occasional spray of silicone.
The most common texturing product I have used is baking soda, what a multi-use product that is, we use it in the home, and commercial cooking, and I used it by the pallet load for my wet cast textured stone. To use it this way it’s necessary to mix a reasonable quantity in a bucket with some clean water, not too much, enough to make it “lumpy”, let it dry just a little, and now it will have different sizes lumps when after a little practice, you can form the perfect texture as the baking soda sticks to the release grease/oils.
Assessing the quality and consistency of each raw material is paramount. A supplier might offer you a great deal, but if their sand has impurities, that deal becomes a liability. Always ask for samples and test the materials in your own mixes.
Conclusion
Building a relationship with suppliers goes beyond the initial purchase. You might find that establishing long-term partnerships with suppliers who offer reliability, transparency, and good communication can greatly benefit your operations. They can work with you on pricing, understand your needs, and ensure a consistent supply.
Remember, your first attempt doesn’t need to be your last. You can always adjust your approach down the road as you discover suppliers that better meet your needs or if your business model evolves.
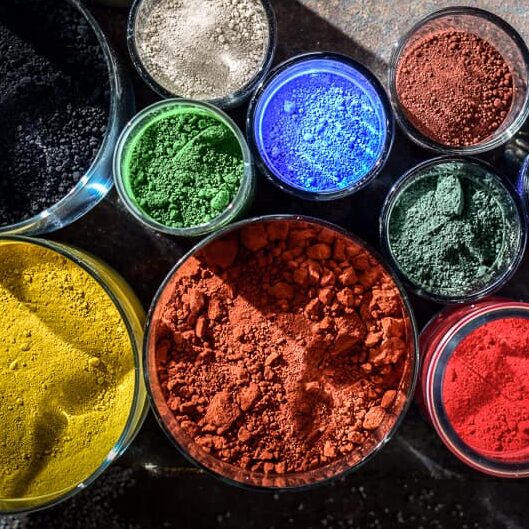
Basic Materials List
- 1, Coarse Sand. or Silica sand
- 2, Small-Sized Aggregate. A 3/8″ to fine silica aggregate.
- 3, Powdered Pigments.
- 4, White Fine Mils Cement.
- 5, Chopped Fibers 3/4″ to 1 1/2″ Long Stranded Prefered.
- 6, Fiberglass Rebar.
- 7, Release Agents. Cooking oil and cooking lard.
- 8, Texturing Products Like Baking Soda.
Future Post
In another post I will go through the production area requirements, I hope you have found this an interesting and detailed breakdown of how and what you need. And don’t forget a nice custom contract with an upfront deposit, that can get you started.
Contact Us
We hope you find the information useful, but if you have any questions or need help with any project, send us a message and we will get back to you. You do have to sign in and confirm these days to comply with government rules. Sorry for the inconvenience.
Thank You Author Rob
This post is incredibly detailed and inspiring, Rob! Your journey from garage-made pieces to a thriving enterprise is truly motivating. I appreciate the practical insights into sourcing materials and the specific advice on what to look for in suppliers. It’s fascinating to hear how even the smallest details, like the purity of white cement, can significantly impact the final product.
I do have a question: Can you share more about the challenges you faced during your initial growth phase and how you overcame them? It would be helpful to understand how you managed both the business and production aspects as you scaled up. Thanks!
Hi Scott,
It would be my pleasure at some point in the near future. Ther are just a few articles in the basic chain that I want to finish. And your request, is probably going to be more than one article as the rapid growth created many.
It’s always interesting to watch people who can take up challenges like that, even if they’re not experts! I’ve always admired people like who could take on a challenge to find all the raw materials to pursue your challenge ahead. I was very interesting in your selection process for raw materials. I too enjoy doing checklists and I also believe in the power of work and determination in everything I do!