Overview of What is Pre Cast Stone

I am going to start with the basics. What is pre cast stone? Architectural cast stone is a bit like a chameleon in the building world. A man-made material designed to mimic natural cut stone. Cast stone has been used for centuries to add elegance and durability to structures. When strolling down the streets around the world, and you see those intricate stone details on buildings, there’s a good chance that this is cast stone at work. An understanding that pre cast stone can be divided into 2 major categories. Architectural cast stone and structural cast stone, may be helpful as there are only a few companies that are involved in the latter.
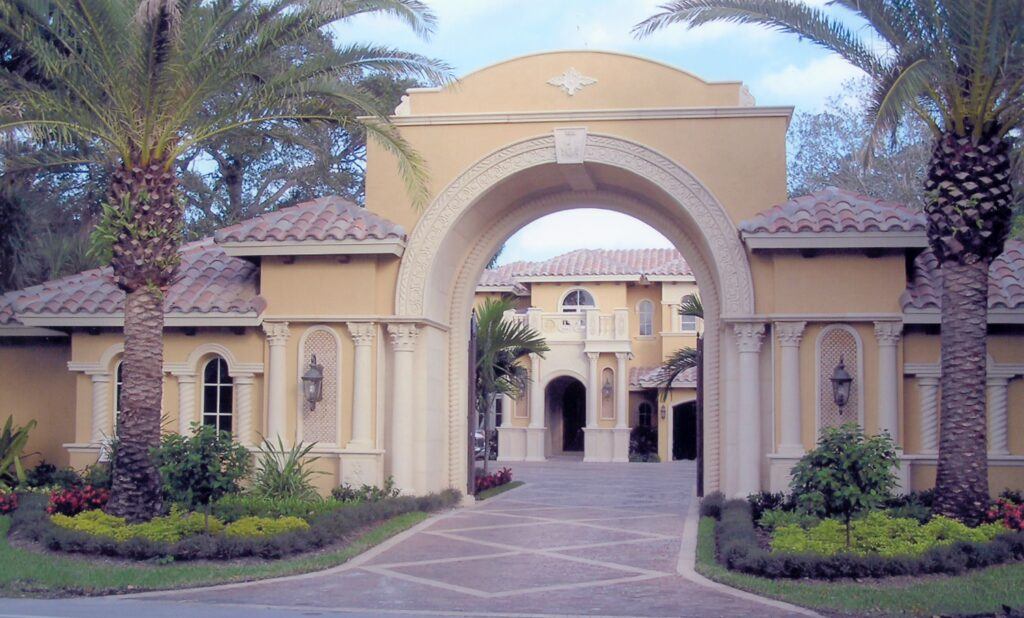
History
So what is pre cast stone, how did it all begin? Some trains of thought believe the use of cast stone has roots as deep as ancient Roman times. But it would appear that reference to the first use of cast concrete in structures like the Coliseum may be correct. But the first real use of architectural cast stone began in 1138 in Carcassone, France. Fast-forward to the late 19th century, and it’s making a resurgence. Why? Because it provided an economical alternative to natural stone, especially during the Gothic Revival architecture movement. It also gained widespread use in America in the 1920s.
But what is pre cast stone and what exactly goes into this product? The primary components are natural aggregates, like crushed stone and sand. These are blended with a binder, usually cement. And coloured pigments are added to the mix to achieve a natural stone appearance. It’s all about creating a high-quality material that not only looks the part but also stands the test of time. It can even be stronger than the product it imitates.
The Art and Science of Manufacturing Cast Stone
Making architectural cast stone is a fascinating blend of creativity and technical precision. Let’s walk you through the process, which transforms a mixture of natural materials into a durable, stone-like building component that both aesthetically pleases and endures over time.
It all starts with the design phase. Here, architects and designers decide on the profiles, shapes, textures, and colours of the cast stone that will feature in their buildings. They may also specify the type of casting that must be used. The 2 most commonly used are Wet Cast and Dry Tamp.
Once all the design elements are approved & signed off, shop drawings are produced, and then a mould or moulds are crafted, typically from wood, rubber, polystyrene or fibreglass, or a mixture of materials to capture every intricate detail the individual design calls for. Some pieces need the artistic talents of a model maker to make a full-size model of the piece required before the mould can be made. The number of pieces that the mould is expected to turn out also plays a part in the choice of the mould material as does the type of casting method used and finish required.
What is Pre Cast Stone And It’s Mix.
In terms of what goes into architectural cast stone, think of it as a gourmet recipe for a faux stone: a mix of high-grade Portland cement, which is most commonly a white cement, fine aggregates, and carefully selected crushed stone, which can vary greatly by geographical location. And don’t forget the admixtures! Some of these are ingredients added to enhance strength, colour consistency, curing time, and in some cases, weatherproofing. Most cast stone incorporates some form of reinforcing, especially the larger pieces.
The ingredients are weighed and then mixed together, in a predetermined order. Most commonly with a regulated batching plant or process to obtain consistency. The mixture is then transported by a wheelbarrow and poured into the various moulds. Depending on the required final finish, it is heavily vibrated to remove air pockets with the wet cast method. Thus ensuring a denser and more uniform product.
With the dry tamp method, the products are vigorously tamped in layers with air tools or by hand and carefully worked into the more difficult areas. It’s not just pouring and waiting either. Quality control tests are run to check for colour uniformity and structural integrity. Some of these tests are taken before others after the stone is cured. In larger facilities, a detailed tracking and system of identification is employed.
Curing and Quality Control.
It isn’t just about creating a natural stone alternative; it’s also about pushing the envelope of what man-made building materials can achieve. The cast stone is cured, and some facilities use a humidity-controlled environment, to achieve optimum strength. Others opt for natural drying. When cured, the product is de-moulded and checked for quality to match the specific requirements of each project, before being palletised and continued curing.
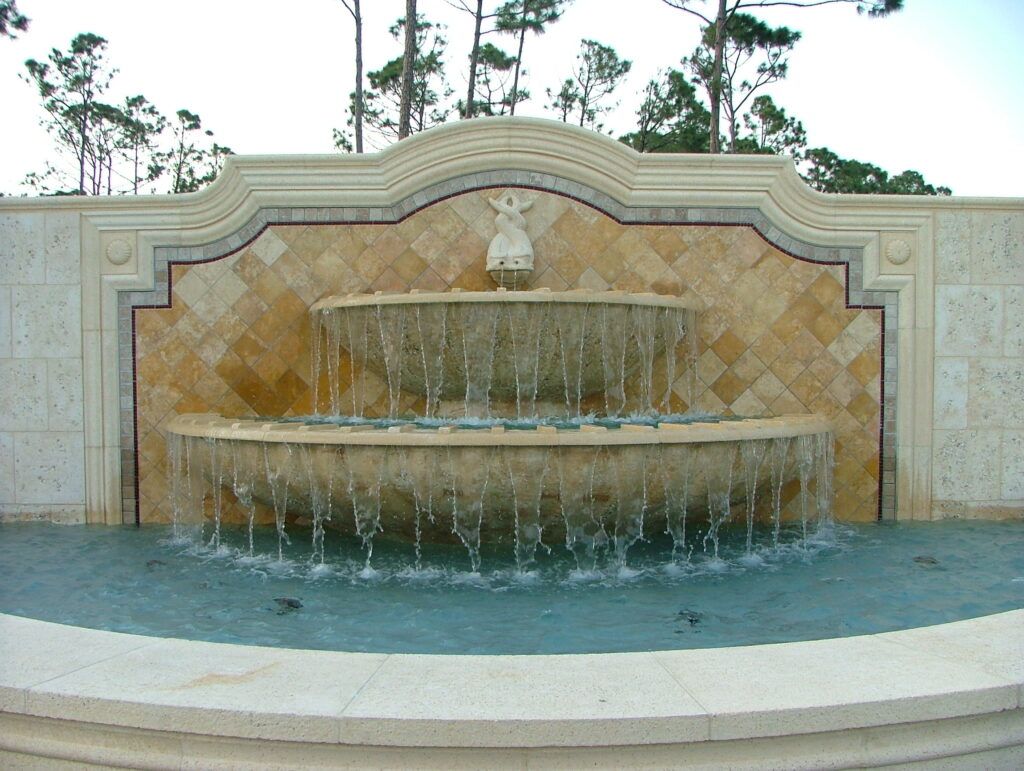
I really hope that you’re beginning to see the intricate craftsmanship behind each piece of architectural cast stone. But how does this engineered material stack up against the genuine article? That’s going to include looking at a variety of factors, from aesthetics to durability and cost.
Cast Stone vs. Natural Stone: A Comparative Analysis
When you’re eyeing the graceful contours of a building, you might find yourself wondering, is that natural stone or cast stone? Good question! The differences between the two can be so very subtle, yet significant.
Visually, natural stone has an unmistakable authenticity that’s harder to replicate. Each piece is uniquely formed by nature, with varied colours and textures. Cast stone, on the other hand, offers a level of consistency and versatility. This allows for uniformity in design and colour matching for restoration projects. But even the natural variances of colour and texture can be replicated at many of the more experienced facilities but at a cost.
What Is Pre Cast Stone And It’s Costing?
Now, let’s talk money. Naturally, the cost factor is a biggie when making a choice for construction materials. Natural stone typically commands a much higher price due to its quarrying, sculpting and transport processes. Cast stone, because it’s man-made and uses cost-effective materials, more often wins as the more budget-friendly option. Wet cast stone is less expensive than Dry tamp. This is especially the case when many pieces of the same item are required. The mold amortisation costs are far more effective than any hand-carved alternate. Even though there are some pretty impressive machines which are taking on some of the aspects of hand carving. But so very expensive.
Maintenance is important in the long-term upkeep of any building. Natural stone is durable but can require more care to preserve its natural beauty and integrity over time. Cast stone, with its highly controlled manufacturing process, generally demands less maintenance and can withstand environmental factors effectively, provided it’s been properly manufactured and installed.
I’m not just talking about durability here; I’m also talking about longevity. Both materials have been known to last for centuries. But it isn’t all about standing the test of time. It’s about preserving the structure’s design, character and integrity throughout the years, and both materials excel in different environments. This leaves us pondering their use in upcoming architectural ventures.
Innovative Uses of Cast Stone in Modern Architecture
When you look around some of today’s most impressive urban landscapes. There’s a good chance you’re admiring the versatile use of architectural cast stone. This material has been shaped and coloured to fit a staggering array of design aesthetics. From the crisp lines of contemporary office buildings to the ornate details of luxury residences.
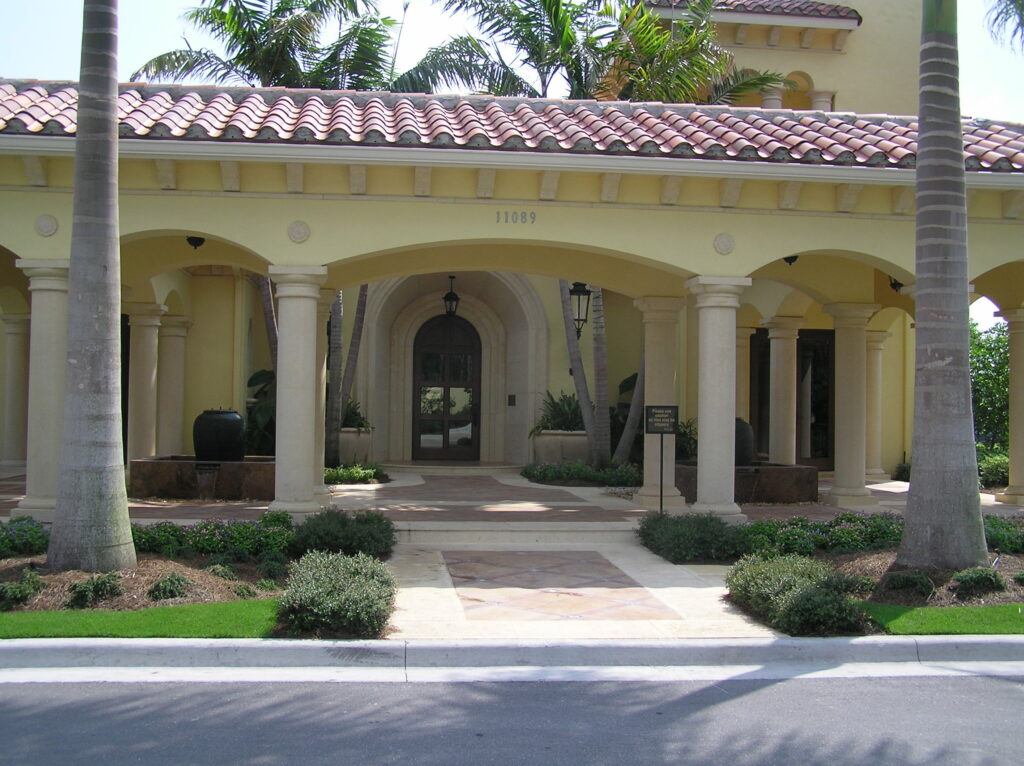
A spotlight on some groundbreaking projects showcases just how adaptive and integral cast stone has become. Elegant bridges, lavish hotel complexes, and even restored historical sites have incorporated cast stone for both its beauty and resilience. The reasonably new Atlantis in Dubai used a GFRC version of a cast stone, very impressive in its looks. A few taps with your knuckles here and there will disappoint you as a hollow sound comes back at you.
Emerging Trends.
Emerging trends are pushing the boundaries of what can be achieved with cast stone. Architects are experimenting with various textures, finishes, and colours to make unique building facades that stand out in a city’s evolving character.
Moreover, as sustainability becomes a primary concern in construction, cast stone is capturing the attention of eco-conscious builders. It offers a long-lasting, low-maintenance option that contributes to the reduced consumption of natural resources. With the trend to incorporate many recycled materials and improve energy efficiency. The future of cast stone in its many forms for building design looks bright.
If you’ve ever wondered about the future of architecture and building materials, cast stone is an innovation to watch. Its ability to mimic other materials, coupled with its unmatched durability, makes it a smart choice for everything from personal homes to public edifices.
Conclusion
And that’s the end of our look at what is pre cast stone. Next time you pass an impressive building, take a moment to appreciate the artful use of this versatile material. Who knows, maybe you’ll be inspired to include a bit of cast stone in your next project.
Contact Us
We hope you find the information useful, but if you have any questions or need help, send us a message. You do have to sign in and confirm these days to comply with government rules. Sorry for the inconvenience.
Author Rob