Cast stone molds.
Step one.
5 steps to Incredible cast stone molds start with the plans, then to the designs, including many assemblies. Then the individual mold shop drawings are prepared based on the signed contract and specified profiles or pieces and quantities. Attached to them are the correct number of custom tags in an appropriate bag. These have barcodes on them to track progress throughout the manufacturing, delivery and installation processes.
This post contains affiliate links. If you make a purchase through these links, I may earn a commission at no extra cost to you.
As an Amazon Associate, I earn from qualifying purchases,
Step two.
The shop drawing is reviewed by the mold shop foreman. He first checks if it is a standard piece, if so he asks one of his staff to go and fetch the molds from their appropriate storage area.
Next, they are checked for any defects and repairs are made or he may request new or additional mold(s). His next task is to see if the shop drawing called for any stop ends to create exact lengths, or left or right profile return pieces. Once the appropriate accessories for the mold were made or just attached from stock, the mold would be scanned as complete and moved into production.
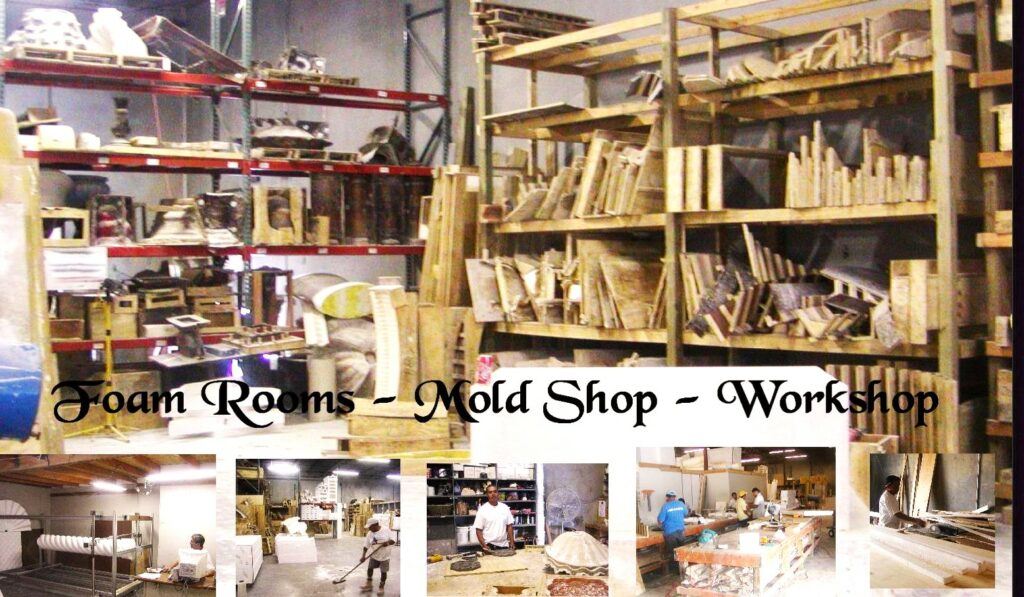
The biggest part of the mold shop foreman’s responsibility in the 5 steps to Incredible cast stone molds is next in the process. If there are no existing molds in stock. He has to evaluate and decide which medium to use for the new mold. First, he has to consider the type of finish required because if it is a normal (for us textured) finish he has more choices, some of which can produce rapid progress. He will also consider if it is to be a temporary mold, how quickly it is needed, the number of pieces required, and the available space in production to pour the final cast stone pieces.
The following are the main sub, 5 steps to Incredible cast stone molds, there are others which can be used in extreme emergency situations. They are not covered here.
The Sub 5 Steps to Incredible Cast stone Molds
- a, workshop
- b, workshop
- c, CNC foam cutting dept
- d, CNC and the workshop
- e, Model dept and workshop
a, He could make a simple frame mold from wood, which would then use the good face of the pouring tables as its main face that shows when complete.
b, A more complex wooden mould using water-resistant good face plywood and other mediums.
c, Refer the shop drawing to the foam machine shop where the cnc machines could cut the molds from expanded polystyrene. They would then send the cut pieces back to the mold shop for secondary assembly. This could include a base or an encasing surround for strength, damage protection or ease of demolding.
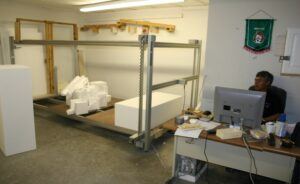
d, Any radius pieces, whether a profile, flat pieces or more complex radius pieces would go through both the mold CNC shop, and then back to the manual hotwire cutting area. Where a special machine with a custom-shaped piece of nickel carbide flat wire was precisely shaped to copy any profile. A lot of these shaped wires came from stock in a locked storage area.
e, Send the drawing to the model shop for its process and the use of RTV rubber, Silicone Rubber, and Fiberglass. And sometimes casting plaster or a combination of all the mediums available. Then the model shop may have to send it back to the workshop area for completion.
In all the scenarios of 5 steps to Incredible cast stone molds, once the molds were complete they would be scanned as completed and moved into the appropriate production area.
The 5 steps to Incredible cast stone molds and their making is an absolutely critical part of creating high-quality cast stone pieces. This quality is then shown in the final finish of any project. With this as the goal it is important to discern which suppliers will best meet your demands for molding materials such as silicone, RTV urethane rubbers, molding plaster and fiberglass & resins. These materials must be top-notch quality to capture the detail and complexity of your designs.
Step 3. Materials & Supplier Evaluation in The 5 Steps to Incredible Cast Stone Molds
In my opinion, 5 steps to Incredible cast stone molds, are the result of making the right choice of medium, using both great materials and possessing the requisite expertise. A substandard mold can lead to defects in the piece and increased costs by affecting the installation and the necessity of new pieces. And most importantly major delays in the completion of the overall project.
Make sure to request product samples or test results to confirm properties like tensile strength, elongation, and tear resistance of major elements, because there are certain countries marketing sub-standard products, so this data is vital for the durability of the molds.
Evaluating supplier flexibility is also essential, especially if you’re working on custom projects. Moreover, look for those who can scale their supplies in response to your production needs without sacrificing quality or causing delays. If you know the delivery parameters upfront then you can run your schedule accordingly.
After locking down trustworthy suppliers of molding materials, you’ll want to zero in on the documentation they provide. The ability to trace materials back to their source. And to have the appropriate MSDS to hand, (material safety data sheet) is not just reassuring, it’s needed for safety procedures, and on occasions of inspections, they contribute to your own credibility and safety measures of your location and business. These details might seem small, but they are significant in maintaining a high-quality production line and facility.
Step 4
When you’re confident with your mold-making material suppliers, you’ll naturally transition to planning for the final stages of your product’s journey – from your workshop to the client. This includes effective storage solutions to maintain the integrity of your cast stone pieces before they’re shipped, along with choosing the right logistics partners. That’s what we’re going to tackle next.
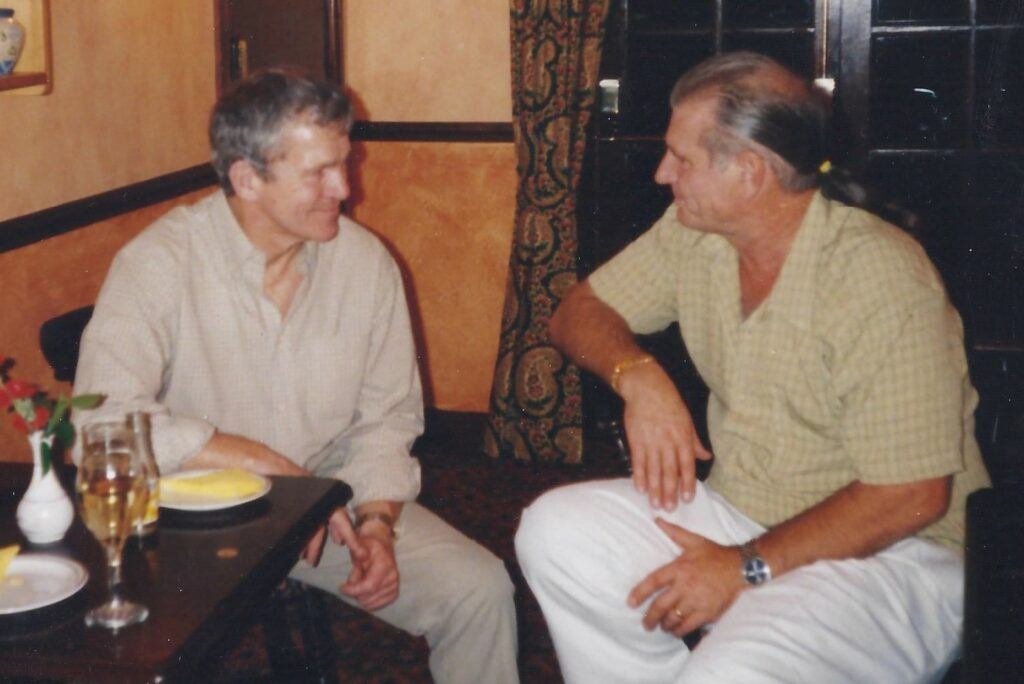
Step 4A,
“The Unseen Hero: My Father-in-Law’s Impact on My Journey”
Often overlooked, holds the key to unlocking meaning. Without it, all other information becomes noise. Let me take you back to my mold shop—a place where creativity melds with craftsmanship, and every piece carries a story. And in the story of the 5 Steps to Incredible cast stone molds, there was 2 people that put this together.
In the manufacturing process, each role plays a vital part in delivering the final masterpiece to our customers. But beyond titles and job descriptions lies the heart of success: a team of multi-talented individuals who think beyond conventions. They are the unsung heroes—the ones who transform raw materials into artistry.
My daily challenges echoed from the mold shop floor. My staff marvelled at my seemingly innate ability to assess any piece, instantly deciphering the best approach. But here’s the untold truth: during those critical years of growth, I had an extraordinary ally—my father-in-law. An unassuming bench carpenter, and more, he possessed a mastery of wood that transcended mere skill. His hands breathed life into furniture, shaping it from the ordinary to the extraordinary.
Yet, his impact extended beyond the workshop. He stepped into the CNC department, overseeing the entire mold shop. His wisdom, like fine-grained oak, infused every decision. And as a father-in-law, he became more—a confidant, a friend, a brother. Our shared passion for work bound us, and we wove memories into the very 5 steps to Incredible cast stone molds that shaped our legacy.
Today, some of those pieces endure, etching their mark on buildings and beautiful works of art. My father-in-law’s name remains unspoken at this point, yet it resonates in every curve, every detail. Perhaps, as I delve deeper into the intricacies of mold making, his story will emerge—a testament to the talent, love, and the quiet strength that shapes our lives.
In the intricate dance of life, some steps remain hidden, yet they set the rhythm for everything else.
I sincerely hope that you can find such a person should you decide to be involved in this industry.
Step 5
A list of equipment and tools needed in the mold shop to allow this to run smoothly
· A good quality table saw, preferably a panel saw.
· A 12” minimum compound miter saw set in an appropriate bench.
· Work tables of with plywood or similar tops, as long as possible for using a large radius arm jig.
· Dust extraction system.
· CNC foam cutting machine(s)
· Computer workstation and the minimum Hardware to draw and run the the CNC machine(s). I have always used Corel Draw and sometimes Auto Cad.
· A radius foam cutting machine.
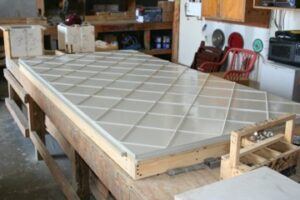
· Storage rack for flat sock materials.
· Drill press.
· A large capability handmade lath for shaping bigger foam pieces, quickly.
· Tool storage cabinets.
· Enough small hand tools per the No of projected workers.
. A scanning station if you have that system.
In a later article, I will go into what and how many of these items are used in the 5 steps to incredible cast stone molds and create a basic material list and their uses. We hope you find the information useful, but if you have any questions or need help, send us a message. You do have to sign in and confirm these days to comply with government rules. Sorry for the inconvenience.
Author Rob
This article on mold-making processes is a fascinating read! I love how it breaks down each step from the initial plans to the final production. It’s clear that a lot of thought and expertise go into creating high-quality molds. The emphasis on using different materials and the detailed decision-making process for selecting the right medium really highlights the craftsmanship involved.Overall, this article provides a thorough and engaging look into the world of mold-making. Great job!
Hey there,
“Love the attention to detail in this post! The process of bringing a design to life is fascinating, and it’s great to see the steps involved in creating a cast stone mold. The combination of artistry and technical skill required is impressive. Thanks for sharing your expertise and giving us a glimpse into the world of cast stone creation. Can’t wait to see the finished product! What inspired the design of this particular mold, and what kind of projects do you envision it being used for?
Marios