
Overview A Hot Wire Foam Cutter
How to understand the intricacies of a hot wire foam cutter machine well. At its core, it’s a tool designed to cut polystyrene foam and similar materials with precision. It uses a heated wire to slice through foam, creating smooth edges and intricate shapes, guided by the user’s design.
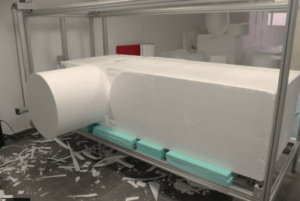
.
I/We promote transparency. This post or site may contain affiliate
links. This means only if you make a purchase through these links, not just by clicking, I/we may earn a small commission at no extra cost to you.
As an Amazon Associate, I earn from qualifying purchases.
I was one of the very first to introduce one of these hot wire foam cutter machines into the industry in Florida. I had gone searching for something that could help me achieve continued quality in my basic molds. Profiles, window sills and bandings, in particular, had been causing me so many problems with the alignment between adjacent pieces. Remember Google was just starting out when I was researching, so it was phone, fax and I think email basics.
Researching For A Hot Wire Foam Cutter
I found what I thought was the right place to go in Atlanta. So the wife and I turned it into a Busman’s holiday! One day looking at complicated high-tech (then) machinery. The next in some small rental boat in a huge swamp with gators everywhere. But it turned out to be one of the best things we ever did. and we ended up with 6. So getting it right the first time is so important. I am hoping to have links to these machines, so stop back from time to time.
How Does A Hot Wire Foam Cutter Work.
So, how does this machine operate? Imagine a tensioned wire, made of materials like nichrome, ( NiCr ) or TitaniumWire. And when it’s heated electronically, it effortlessly melts through foam. The heat is adjustable, allowing for control over the cutting speed and heat. For the density of the material and the detail of the piece being worked on.
Applications.
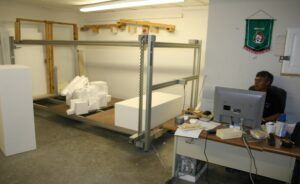
You might be wondering about the practical applications of such a tool. They’re very varied. From architectural modelling, creating prototypes, cutting different thicknesses of insulation. Turning pieces (forms) for builders or shell contractors, and designing props for theater and film. To crafting intricate artwork, sign making or making large quantities of profiles for stucco/plastering contractors. And that’s just scratching the surface.
Do not.
About right here is an appropriate spot to bring up a big NO. Don’t do what I did and waste a load of money on a machine that’s not suited for this industry. Not so much the hot wire machines, but when I went one step further and bought a MULTICAM CNC router.
For over $120,000, to take over all of the flat radius work. To the same accuracy as the hot wire machines did concerning the straight work.
What a waste that was, the machine kept breaking down due to static issues and its inability to deal with the milled waste. Which clogged everything up, even with the extraction system in place. Not made for the job and customer service was not adequate.
Complexity.
And, I didn’t figure in the new complexity of the 3D software, and the costs involved in finding or teaching staff with suitable skills how to run it. Even with the company’s promises of a great resale market, I ended up getting rid of it for about 10% of what I paid for it. And the time and materials that were wasted along the way.
There are now great machines out there for this task, but the software learning curve still exists, it’s not as bad as it was though.
As we talk about these cutting-edge tools, I intend to offer you insights based on expertise, and authoritativeness. I bring forth the latest in technological developments, practical advice, and the nuances of the machine operations—all framed with a consideration for what is most helpful to you.
Types, Sizes, and Necessary Skills for A Hot Wire Foam Cutter Machine
A hot wire foam cutter machine come in various shapes and sizes, each tailored to specific tasks. From handheld tools to large industrial machines, the spectrum of choices can be overwhelming. In this section, I’ll help you break down the options and help to match the right machine to your project’s needs. It’s important to note that larger machines generally offer more flexibility by being able to cut more than 1 block at a time or just bigger block sizes, we ran 6 machines at one point. Earning money while we slept, I wonder if you have figured out how? But they also require more space and a lot bigger investment.
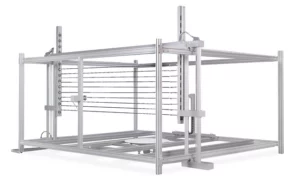
To the rescue.
Thank goodness I had my father-in-law, Brian beside me at this stage, he eventually took over all of that responsibility for me, so I could develop the software program for operating the whole show. He made these machines to more than the manufacturers had thought of at that time with his creative carpentry and workshop jigs.
Foam Selection.
When selecting a machine, consider the thickness and density of the foam you intend to cut. Most blocks of foam purchased in the past have been 2.4 x 1.2 x 1.05 (8′ x 4′ x 3′ 6″) but the sizes do vary depending on the supplier. And normally the smaller the block the more per cubic foot you will pay.
Handheld models are ideal for artists and hobbyists working on smaller scales. These are typically more affordable and easier to manage but even commercial operations have their uses for these tools too. For industrial purposes, consider a larger, stationary machine that can handle heavy-duty cutting, (meaning long periods of operation), tasks with ease. The size of your workspace will also play a major role in your decision. The larger machines require a dedicated area, not just for the machine but so you can safely load the machine. And you should always have plenty of dry storage space for a large amount of additional blocks.
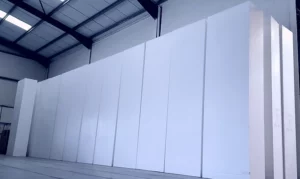
Operating The Hot Wire Foam Cutter Machine.
Operating a hot wire foam cutter requires a blend of technical knowledge of the computer and apps. and the creative skills of a good finish carpenter. While these machines are not overly complicated in themselves, familiarity with basic electrical safety and tool handling is essential. Many machines on the market today can work with just a simple wired remote, But they require the drawing files prepared separately in .PLT or .DXF format for the machine to work.
This means that it’s best to have a localised computer workstation either a PC or laptop if you have the space available. You then have control over the drawing and operation of the machine and can stop the operation should something not be right. If working hand-held or manually operated cutters then a dexterous hand figures prominently in achieving clean operation.
New Too Hot Wire Foam Cutter Machines?
If you’re new to using a hot wire foam cutter, it’s best to start with some very simple designs and work your way up as your confidence grows. Most manufacturers provide sample drawings and simulations that show you if you prepared your drawings correctly. They normally have instructional videos on basic handling of the controls and how to use the software incorporated in them for their machines. I recommend you study them in detail before you begin and run simulations you will find them very beneficial.
Additional Software.
I evolved with Corel Draw as my main program of choice for design as I was introduced to it several years before. And I knew my staff could become competent in the programs in a shorter period than say, CAD. Depending on your intended use of these machines, you may need to become competent in nesting as well. The biggest learning point we came across at this stage was not understanding that whatever shape/profile you were drawing, you made sure you connected all the outlines as one shape, otherwise the machine cutting software would make its determination and would shoot off on its own, predetermined direction, ruining your mold.
Nesting is another common word used in foam cutting, I will discuss this term and other relevant topics in a later article around technology and the relevant needs in the precast industry.
Setting Up The Hot Wire Foam Cutter Machine.
Beyond the cutter itself, being set up in a very level and square configuration, some machines require you to build and install a level working bed in a way that does not affect the operation of the machine. No matter what configuration you intend to use it in, Lathe or turntable on the 3rd axis, this adaptation is particularly important, especially if you need to cut many smaller pieces.
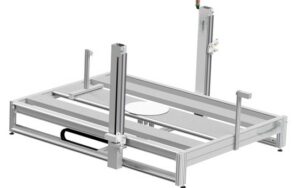
3RD Axis.
Nearly all of today’s hot wire foam cutter machines offer a 3rd axis, which means you can expand your ability to use a turntable or lathe operation, enhancing your portfolio of pieces you can make while expanding your cutting experience. This can be an extra on many models, both for the machine and the controlling unit. Even if you can’t stretch to the additional parts for the machine, you should ask about the controller. Because you might have to buy another one of them, should you expand later?
Tapered Cuts With A Hot WIre Foam Cutter.
Another advancement is the ability to cut tapered pieces. This is a very useful function and one worth exploring before you buy. In layman’s terms, it just means that one end of the wire is moving differently from the other end. It sounds very simple when I say it that way. But in reality, it’s a more complicated process to make the machine complete the task. It’s not just the software, it is some of the mechanical parts of the machine. Allowing the wire to shrink and contract without ruining the quality of the cut. And the independent movement of the stepping motors and their rails.
Basic Accessories.
Basic hand-held tools, which you do need for model prototyping and free-forming are needed, and some form of radius cutter that you can adapt depending on your intended uses, the maximum profile size and the radius of the pieces you expect to cut, is another absolute must.
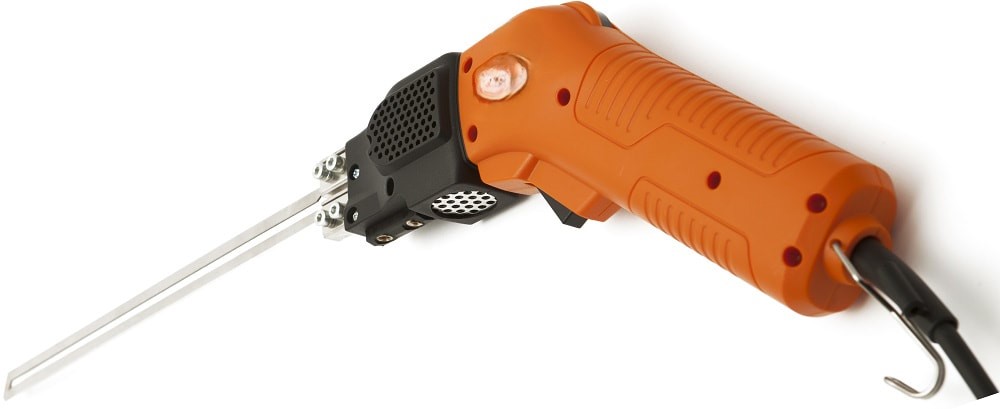
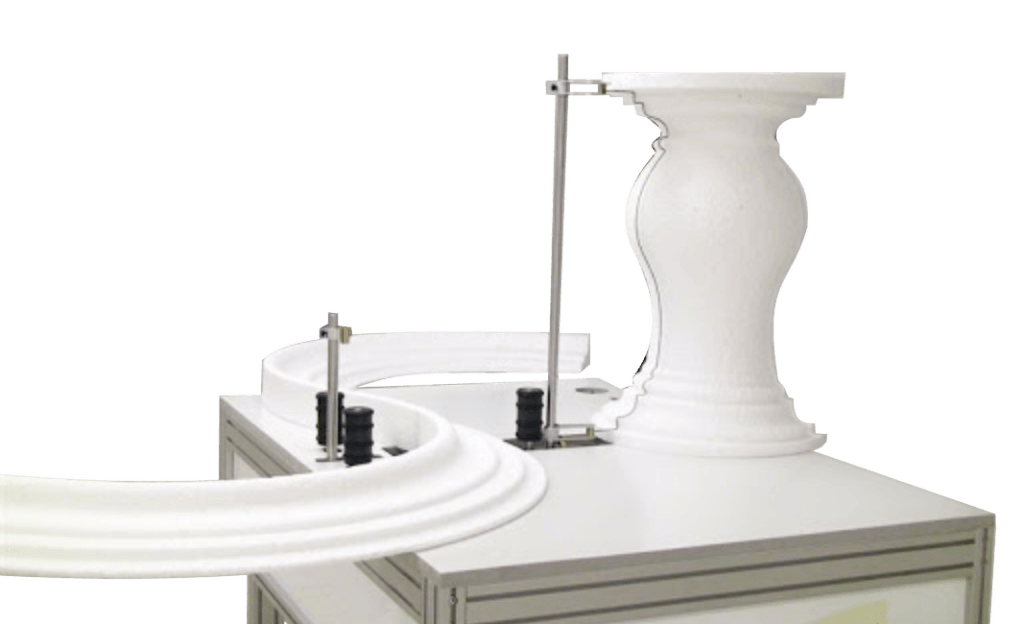
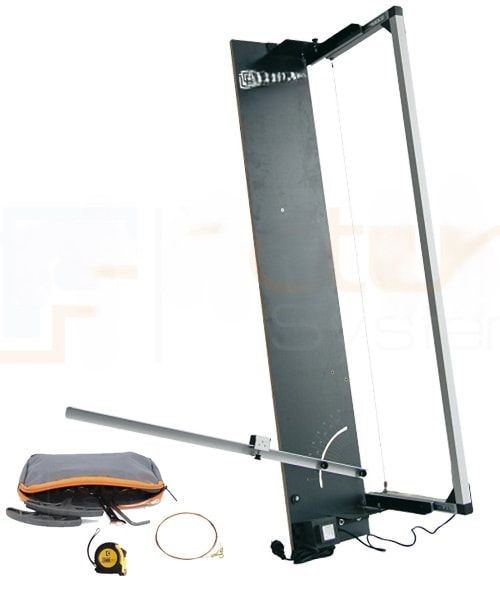
Some small machines on the market today require specialized cutting tables, guide rails, and foot pedals if you require a hands-free operation. These are just a few of the accessories that could improve precision and safety, but most I would steer away from if you need precision.
Software. Corel Draw.
As for software, programs that allow for design and layout planning. That can also be connected to computer numerical control (CNC) cutter controllers for automated cutting. Software like Corel Draw is the way to go. I am still using my Corel 16 version. There’s no need to go for the latest and greatest version until you at least know how to use it. Or perhaps you have a need to use other parts of the suite. Most of the latest versions do not really have anything that suits the needs used in this application.
Other Software.
SketchUp may be a suitable 2nd place, and Adobe Illustrator or Auto CAD programs are commonly used for drawing at a far higher level and there is a far greater learning curve so I do not recommend them for this task unless you are already familiar with them. Corel’s DXF file output gives you the accuracy that is best suited. They can all do the task of translating designs into cutting paths for the machine to follow, but if you are new to the process you do need to allow yourself plenty of time to learn these processes.
Next, I will inform you of the materials these versatile machines can work with and spotlight the premium choice for precast mold making. Remember, choosing the right material isn’t just about what can be cut; it’s about achieving the desired finish and durability for your project.
Materials, Molding, and Mastering A Hot Wire Foam Cutter
To guide you through the varied world of materials that you can cut with a hot wire foam cutter, zeroing in on the specifics for those in the mold-making scene. When considering your options, remember that not all foams are created equal. The most common types you’ll encounter include;
- polyurethane foam – PU
- polypropylene foam – PP
- polyethylene foam – PE
- mineral wool, rock wool, but also EPS, XPS, EPP, foamed glass, etc.
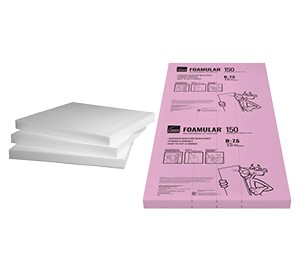
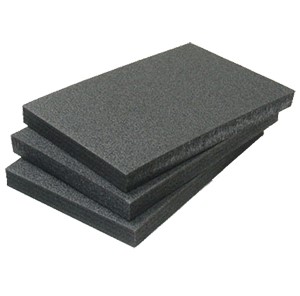
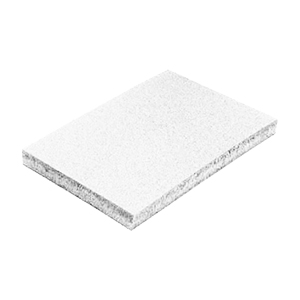
EPS Foam.
For those with a keen interest in precast mold making, EPS (Expanded Polystyrene) foam comes highly recommended and the normal choice for most manufacturers that use this type of mold-making option. Its uniform structure and density make it an excellent candidate. It carves cleanly, ensuring crisp details and a smooth finish that are crucial for professional-looking molds and finished pieces.
The foam we used 99% of the time was 1.35 to 1.80 pounds per cubic foot (21.6 to 28.8 kg/m3). This is either Type II or Type IX EPS according to ASTM C578 We did on occasion go for a little denser foam for special projects where more strength in the mold integrity was required, using it for standard profile mold, we had issues with curling.
Virgin Foam.
And most importantly it must be VIRGIN foam, why because if the block you were cutting contained a recycled product it would at the very least damage the surface of the mold you would be pouring against, and at worst, leave you with a mold and a block of foam that you could not use.
The Use Of These Hot Wire Foam Cutter Machines.
Mastering the use of a hot wire foam cutter is more than about understanding the machine; it’s about learning the software for precision in your designs, practice, and patience.
Start with simpler designs and gradually move to more complex patterns, using the 3rd axis and learning Nesting as your confidence and skills grow. Regularly cleaning the wire and ensuring proper tension if your machine does not have automatic tensioning, is a task that can have a significant impact on your cutting accuracy. Because my father-in-law was a great craftsman he adapted better than everyone and he enjoyed it.
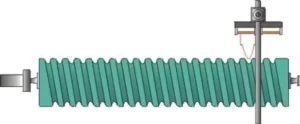
Maintenance.
In terms of maintenance, your hot wire foam cutter is no different from any other tool in your workshop. Simple habits such as keeping the cutting wire clean, checking for wear and tear on any drive belts and bearings, watching out for any static build up and we found it best to blow out the rails with the compressed air, but this should be done with care, ensuring the workspace is free from unnecessary debris will also help to keep your machine running smoothly for years to come.
A Hot Wire Foam Cutter Makes Waste And Recycling Important.
One point that really needs to be addressed early is to plan for the waste factor, no matter what foam you use. Today there are more machines available for recycling which is now a common practice. We strongly recommend that you look at one form of machine or another, early in your operation because it does very soon pile up, more than wooden waste in a woodworking shop. Most suppliers have implemented recycling programs. There are now more uses for recycled foam so it could help towards the costs and be environmentally friendly.
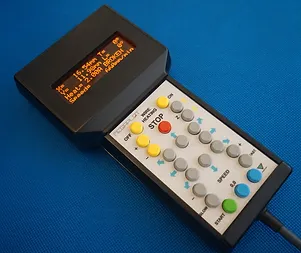
User Experience.
Finally, let’s acknowledge the heart of the matter, the user experience. Whether you’re a seasoned professional or a hobbyist just starting out, understanding and utilizing your hot wire foam cutters should be straightforward. Manufacturers are advised to and do provide clear instructions, tutorials, and customer support, making the tool accessible to all skill levels.
New machines are normally supplied with some or all of the following, Touch Screen, Shaper software, Windows Software, Remote Control and lots of instructions and access to customer service.
Contact Us
We hope you find the information useful, but if you have any questions or need help, send us a message. You do have to sign in and confirm these days to comply with government rules. Sorry for the inconvenience.
Author
Rob
Hello,
This post on hot wire foam cutters is a treasure trove of practical insights and personal experiences in the industry. Your journey from discovering the technology in its infancy to mastering its applications for mold-making and beyond is fascinating.
Your advice on machine selection, operational techniques and the importance of material choices is invaluable for anyone looking to delve into foam cutting. The candid sharing of successes and pitfalls adds authenticity, making this a compelling read for both novices and seasoned professionals alike in the field of foam cutting and mold-making.
Thank you for sharing this post.
Great article on the intricacies and practical uses of hot wire foam cutters! Your detailed explanation and personal anecdotes make the topic very engaging and informative. I particularly appreciate the advice on starting with simple designs and gradually moving to more complex ones as confidence grows.
A few questions come to mind:
1. **Maintenance Tips:** You mentioned the importance of regular maintenance. Could you provide more detailed steps or a checklist for maintaining these machines to ensure longevity and precision?
2. **Software Learning Curve:** What resources or training programs would you recommend for beginners looking to get up to speed with the necessary software for operating these cutters?
3. **Material Recommendations:** For someone just starting, is there a specific type of foam you’d recommend for practice before moving on to more expensive or specialized materials?
4. **Waste Management:** You highlighted the issue of foam waste. Could you elaborate on effective strategies for managing and recycling this waste?
Looking forward to more insightful articles on this topic! Thanks for sharing your expertise.
cheers Graham
Hi Graham, and thank you for your comments. With regards to question 1, it’s hard to answer as it is machine-specific. The basics for the machines I am familiar with were included in the post.
2, Software is not an easy question, but Corel Draw offers a student program, so does Autodesk and Adobe. I think it depends on where the person would ultimately want to go with their training. For this application, I discussed Corel Corel Draw would have the shortest learning curve.
Again I did mention my recommendation, but it does depend on what is readily available, but EPS is the easiest to start with.
Waste Management is again based upon the intended volume, your original supplier, as some have a recycling program or local resources. The best way is to optimise the use of your foam is by coming up with projects that utilise the larger pieces like modelling, you could even find a secondary income stream taking that approach.
I hope this helps you further in your exploration.